The Comprehensive Guide to Hydraulic Balls
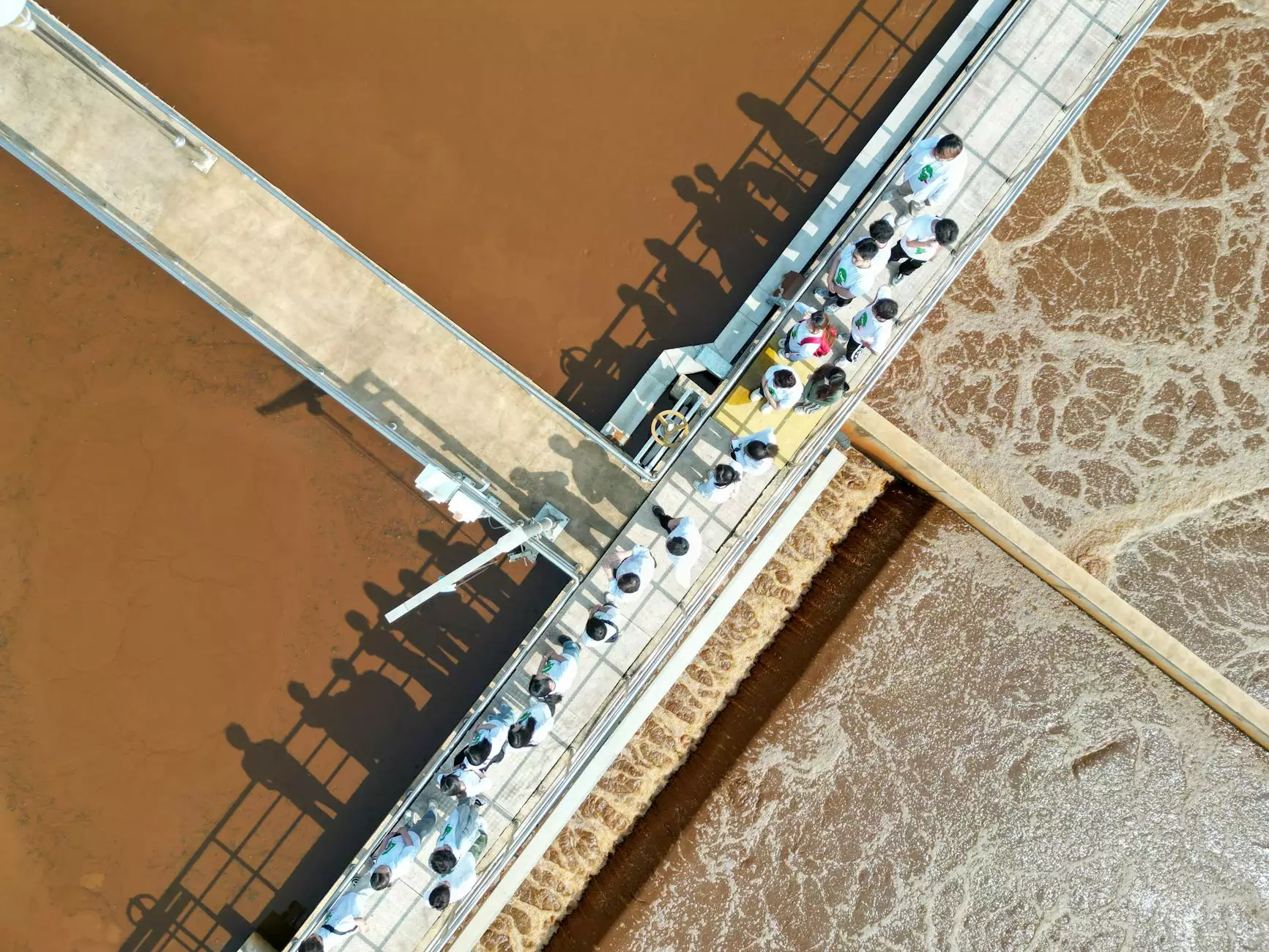
In the realm of industrial components, hydraulic balls play a crucial role in various applications, ensuring the smooth operation of hydraulic systems. This article delves into the intricate details surrounding hydraulic balls, discussing their functionality, types, applications, and the significance of proper fittings in optimizing performance.
What is a Hydraulic Ball?
A hydraulic ball refers to a spherical component used in hydraulic systems. Its primary function is to control the flow and direction of hydraulic fluid, essential for the operation of machinery and equipment. These components are widely used in industries from automotive to aerospace, making them vital for success and efficiency in operations.
The Anatomy of Hydraulic Balls
Understanding the anatomy of hydraulic balls is fundamental. Here are the key elements:
- Material: Typically made from stainless steel, brass, or plastic to withstand high pressure and corrosion.
- Size: Available in various diameters, allowing flexibility in application depending on the system’s requirements.
- Surface Finish: Polished finishes help reduce friction and enhance flow characteristics.
How Do Hydraulic Balls Work?
Hydraulic balls work on the principle of fluid dynamics. When hydraulic fluid enters a system, the ball can either allow or prevent the flow of fluid, acting as a valve. This mechanism is crucial in applications where precise control of fluid flow is necessary. The functionality can be further understood by looking at the following processes:
- Sealing: The ball seals against the seat in the valve to block flow.
- Flow Control: When the ball rotates, it can either allow or restrict flow through its cavity.
- Pressure Regulation: By controlling flow, hydraulic balls help maintain consistent pressure within the system.
Types of Hydraulic Balls
Several types of hydraulic balls can be categorized based on their design, functionality, and application. Understanding these types can help in selecting the right component for specific needs:
- Standard Hydraulic Balls: Commonly used for general applications.
- High-Pressure Hydraulic Balls: Designed to withstand extreme pressures commonly found in heavy machinery.
- Corrosion-Resistant Hydraulic Balls: Made from materials that resist rust and corrosion, ideal for outdoor environments.
- Custom Hydraulic Balls: Tailored for specific applications based on unique requirements.
Applications of Hydraulic Balls
The use of hydraulic balls spans across various industries, showcasing their versatility and necessity. Below are some notable applications:
1. Automotive Industry
In the automotive sector, hydraulic balls are essential components in systems such as power steering and brake actuators. They ensure seamless flow and handling of fluids, crucial for vehicle safety and performance.
2. Aerospace Engineering
In aerospace applications, hydraulic balls help manage hydraulic systems for landing gear and control surfaces, ensuring reliability during flight operations.
3. Manufacturing
Hydraulic balls are integral to manufacturing processes where hydraulic systems are used for lifting, molding, and processing materials. They enable precise control over machinery operations.
4. Construction Equipment
Hydraulic balls are commonly found in construction equipment such as excavators and lift trucks, where they facilitate the operation of hydraulic pumps and cylinders, translating into enhanced productivity on site.
Why Quality Matters in Hydraulic Balls
Choosing quality hydraulic balls is not merely a matter of preference; it directly influences the overall efficiency and safety of hydraulic systems. Here are significant reasons why quality is paramount:
- Durability: High-quality materials enhance the lifespan of hydraulic balls, reducing the frequency of replacements.
- Performance: Quality components ensure optimal flow and pressure management, preventing system failures.
- Safety: In high-pressure applications, inferior materials can lead to catastrophic failures, posing safety risks.
Fittings for Hydraulic Balls
At fitsch.cn, we offer a range of fittings for sale that are designed to work seamlessly with hydraulic balls. Proper fittings are crucial for ensuring that hydraulic systems operate efficiently and safely. Key types of fittings include:
- Threaded Fittings: Allow for secure connections between components.
- Flared Fittings: Provide a strong seal and ease of disconnection.
- Compression Fittings: Ideal for easy installation and repair without the need for special tools.
Choosing the Right Hydraulic Ball for Your Needs
Selecting the perfect hydraulic ball for your specific application requires a careful assessment of several factors:
- Pressure Rating: Ensure the ball can handle the maximum pressure of your system.
- Material: Choose a material that aligns with the environmental conditions and fluid type used.
- Size: Selecting the appropriate diameter is crucial for ensuring optimal flow and compatibility.
Maintenance of Hydraulic Systems
To prolong the performance and reliability of hydraulic balls within a system, regular maintenance is vital. Here are some maintenance practices to consider:
- Regular Inspections: Check for wear and tear, leaks, and signs of corrosion.
- Fluid Management: Ensure that hydraulic fluid is clean and at the optimal level.
- Prompt Repair: Address any identified issues immediately to prevent further damage.
Conclusion
In conclusion, hydraulic balls are indispensable components that influence the efficiency and functionality of hydraulic systems across various industries. From their design and functionality to their applications and maintenance, understanding hydraulic balls empowers businesses to select the right components for their hydraulic needs. For high-quality fittings and components, visit fitsch.cn and ensure your hydraulic systems operate at peak performance.