Unlocking the Potential of Electric Injection Molding in Metal Fabrication
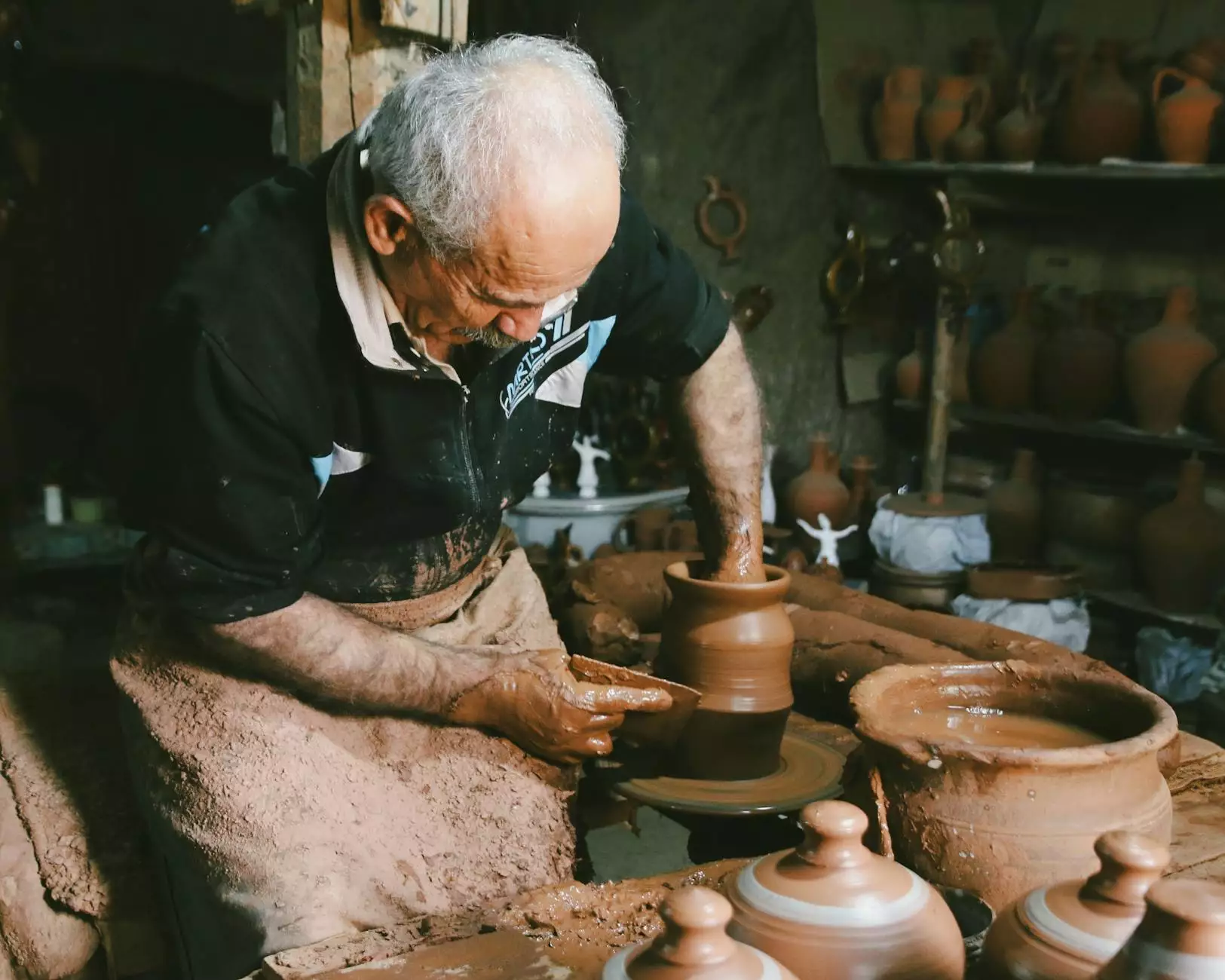
In the world of manufacturing, the advent of electric injection molding has revolutionized the way products are designed and produced. This innovative technology is reshaping the landscape of metal fabrication, offering unparalleled precision, efficiency, and environmental sustainability. As industries evolve and demand for high-quality components rises, understanding the benefits of electric injection molding becomes imperative for businesses aiming to maintain a competitive edge. This article delves deeply into the intricacies of electric injection molding, its advantages, applications, and its transformative impact on the future of manufacturing.
What is Electric Injection Molding?
Electric injection molding is a modern manufacturing process that utilizes electric motors to drive the injection unit and clamping mechanisms instead of hydraulic systems. This shift from traditional hydraulic to electric systems offers numerous benefits, making electric injection molding a preferred choice for many manufacturers.
The Mechanics of Electric Injection Molding
In electric injection molding, a precise combination of innovative technology and state-of-the-art machinery is employed. The key components include:
- Injection Unit: This unit melts the plastic or metal raw materials and injects them into a mold. The use of electric motors ensures precise control over the injection speed and volume.
- Clamping Unit: Electric motors are responsible for controlling the mold opening and closing, providing consistency and accuracy.
- Control System: An advanced computer control system monitors and adjusts the entire process in real-time, ensuring optimal conditions for high-quality outputs.
Advantages of Electric Injection Molding
Electric injection molding presents a plethora of advantages that position it ahead of traditional hydraulic systems. Here are some of the standout benefits:
1. Enhanced Precision and Accuracy
The precision of electric injection molding is unparalleled. With electric motors allowing for fine-tuned control, manufacturers can achieve tighter tolerances and more intricate designs. This accuracy is crucial in industries such as aerospace, automotive, and medical devices where small deviations can lead to significant failures.
2. Improved Energy Efficiency
Electric injection molding machines use up to 70% less energy compared to their hydraulic counterparts. The reduced energy consumption not only translates to lower operational costs but also aligns with global sustainability efforts to reduce carbon footprints. In an era where energy efficiency is paramount, electric injection molding stands out as a forward-thinking choice.
3. Reduced Cycle Times
Due to faster response times and reduced mechanical inertia, electric injection molding machines often result in shorter cycle times. This enhances productivity and allows for higher output rates—critical for businesses striving to meet increasing market demands.
4. Consistent Quality
With fewer moving parts and more consistent process control, electric injection molding produces highly consistent final products. Quality control becomes easier, minimizing defects and enhancing the overall reliability of manufactured parts.
5. Lower Maintenance Costs
Electric machines generally require less maintenance due to fewer moving parts and lower wear and tear. This reliability and durability can lead to substantial savings in maintenance costs over the lifespan of the machinery, making it a smart long-term investment.
Applications of Electric Injection Molding
The versatility of electric injection molding makes it applicable across various industries. Here are some key sectors where its benefits are particularly noteworthy:
Aerospace Industry
The aerospace industry demands high precision and reliability. Components produced through electric injection molding can meet stringent regulations and performance requirements, leading to enhanced safety and efficiency in aerospace applications.
Automotive Manufacturing
In the automotive sector, electric injection molding is used to produce components that require high durability and precision. From interior fixtures to critical engine parts, the reliability of electric injection molding contributes to the efficacy and safety of vehicles.
Medical Devices
The medical industry calls for components that adhere to strict hygiene and precision standards. The consistent quality and reduced contamination risks associated with electric injection molding make it the ideal choice for medical device manufacturing.
Consumer Electronics
The rise of consumer electronics has increased the demand for smaller, more complex components. Electric injection molding allows manufacturers to produce intricate parts that fit seamlessly into various electronic devices.
The Role of Electric Injection Molding in Sustainable Manufacturing
As the world shifts towards more sustainable manufacturing practices, electrical injection molding significantly contributes to this journey. Here are ways it enhances sustainability:
1. Reduced Waste
Electric injection molding minimizes material waste through more precise feeding and injection processes. As manufacturers strive for zero waste goals, this technology supports environmentally friendly production practices.
2. Lower Carbon Emissions
The energy-efficient nature of electric injection molding translates into reduced carbon emissions. Utilizing electric power instead of hydraulic systems means lower greenhouse gas emissions, aligning with global efforts to combat climate change.
3. Circular Economy Recognition
By enabling manufacturers to produce high-quality parts that last longer, electric injection molding supports a circular economy. Companies can utilize high-quality recycled materials, thereby reducing the need for virgin plastics and metals.
Investing in Electric Injection Molding Technology
Transitioning to electric injection molding can be a pivotal investment for manufacturing businesses. Here are some considerations for companies contemplating this shift:
1. Evaluating Needs and Goals
Before adopting electric injection molding, businesses should assess their specific needs and production goals. Understanding the factors that drive efficiency and quality in their operations is crucial for making informed investment decisions.
2. Training and Skill Development
To maximize the benefits of electric injection molding, training employees on the intricacies of operating these advanced machines is essential. Ongoing training ensures optimal machine performance and enhances overall productivity.
3. Collaborating with Experts
Partnering with experts in electric injection molding can provide valuable insights and guidance. Collaborations can lead to customized solutions that fit unique manufacturing requirements, driving innovation and efficiency.
Conclusion: Electric Injection Molding as the Future of Metal Fabrication
The future of manufacturing lies in the adoption of innovative technologies that prioritize precision, efficiency, and sustainability. Electric injection molding stands at the forefront of this evolution, offering compelling advantages that resonate across diverse industries. From improving product quality to enhancing environmental sustainability, the transition to electric injection molding is not merely a trend—it's a pivotal movement towards a more advanced and responsible manufacturing landscape.
As businesses like deepmould.net lead the charge in embracing these technologies, the potential for innovation within metal fabrication is boundless. Embracing electric injection molding today can position companies not only to compete in the market but also to become pioneers in the sustainable manufacturing revolution of tomorrow.