The Essential Parts of a CNC Lathe: A Comprehensive Guide
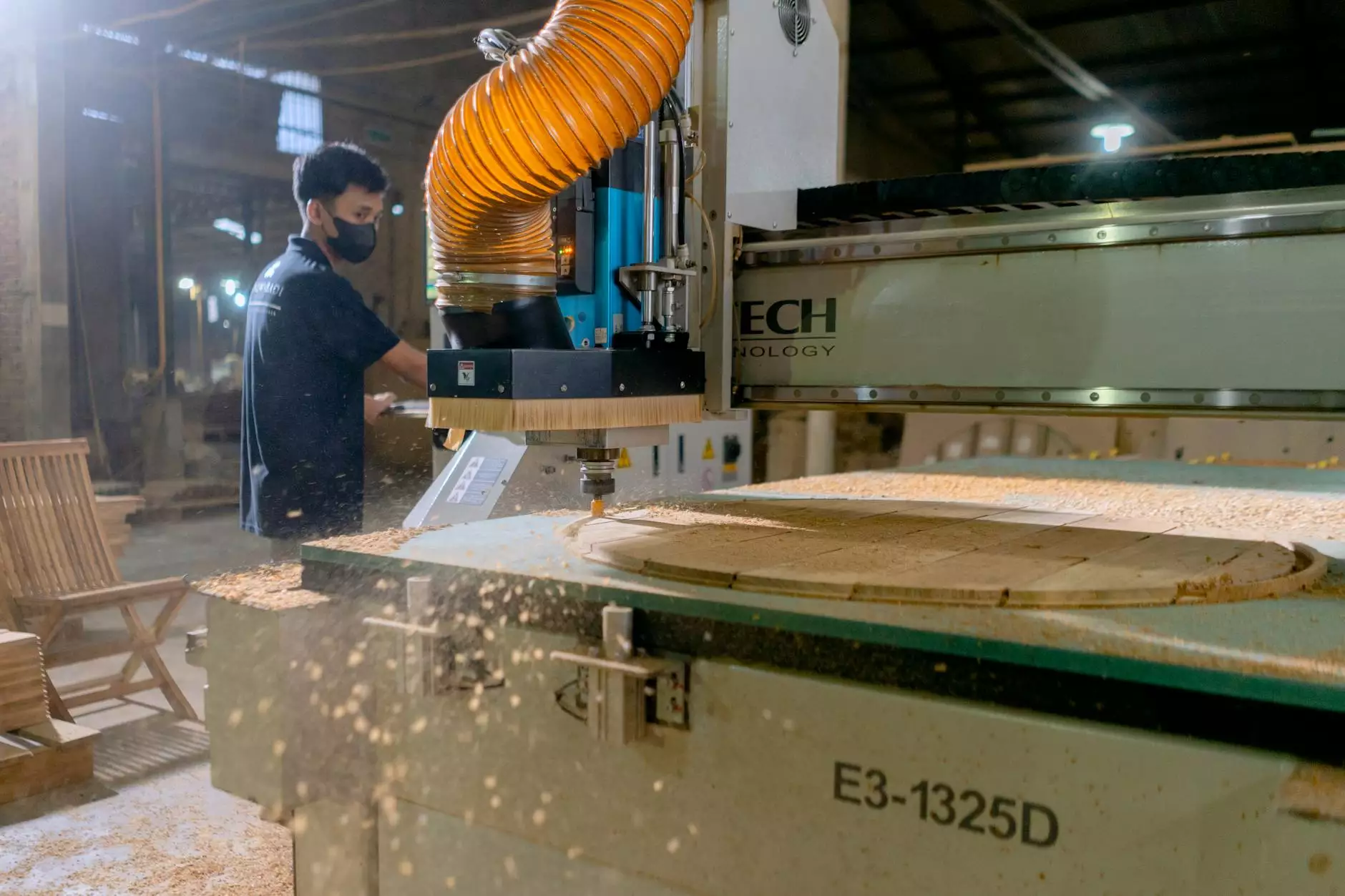
In the world of manufacturing and metal fabrication, CNC lathes play a pivotal role in producing high-precision parts. Whether you are a seasoned engineer or a newcomer to the field, understanding the parts of a CNC lathe is crucial for optimizing your machining processes. This article delves into each component, explaining its function and importance in the context of metal fabrication.
What is a CNC Lathe?
A CNC lathe (Computer Numerical Control lathe) is a machine tool that automates the turning process to produce cylindrical parts. By intricately controlling the tool movements via a computer, CNC lathes enhance accuracy, repeatability, and efficiency in manufacturing. With the advancement in technology, these machines have become indispensable in various industries including aerospace, automotive, and medical device manufacturing.
The Main Parts of a CNC Lathe
Understanding the parts of a CNC lathe allows operators to troubleshoot, maintain, and optimize these machines effectively. Below is an exhaustive overview of the principal components.
1. Bed
The bed is the foundational structure of a CNC lathe and provides support for all other components. Typically made from cast iron or granite, the bed must be rigid and stable to absorb vibration and maintain accuracy during operation. It ensures that all parts remain aligned and function effectively.
2. Spindle
The spindle is a critical component that holds the workpiece and rotates it at high speeds. Spindles come in various designs, such as fixed or variable speed, and their quality directly impacts the precision of the cutting process. A robust spindle enables efficient machining, particularly for complex and intricate designs.
3. Tailstock
The tailstock supports the far end of a workpiece during machining, preventing flexing that can lead to inaccuracies. It can be adjusted along the bed, allowing for different lengths of material. Many tailstocks are equipped with a quill that can hold tools for drilling or other operations, expanding the machine's versatility.
4. Tool Post
The tool post is where the cutting tools are mounted. This component must be adjustable to accommodate various tool lengths and angles, ensuring optimal cutting conditions. Tool posts can be manual or automatic, with CNC models allowing for tool changes on the fly without manual intervention, thus reducing downtime.
5. Carriage
The carriage moves horizontally along the bed, guiding the tool post towards the workpiece. It can be operated manually or controlled via the CNC program, moving smoothly to execute precise cuts. The design of the carriage often includes ways to minimize friction and wear, enhancing overall performance.
6. Lead Screw
The lead screw is responsible for translating the linear movement of the carriage into the rotational movement of the spindle. Precision in the lead screw is essential for ensuring that the tool moves accurately along the length of the workpiece, facilitating consistent and high-quality machining.
7. Control System
The control system is the brain of the CNC lathe. It interprets the computer-generated code (G-code) and translates it into movements of the various components of the machine. Modern CNC lathes feature sophisticated control systems that offer user-friendly interfaces, real-time monitoring, and advanced editing functions.
8. Power Supply
The power supply provides the necessary electrical power to all of the CNC lathe's components. It must be reliable and robust to handle the high demands inherent in metal fabrication processes. Many CNC lathes operate on three-phase power to ensure that there is ample power for motors and other systems.
9. Chip Removal System
The chip removal system is essential for maintaining a clean working area during machining operations. This system transports metal shavings and chips away from the cutting area to avoid interference with the machining process, thereby enhancing safety and ensuring consistent work quality.
10. Safety Features
Modern CNC lathes are equipped with an array of safety features, such as emergency stop buttons, protective shields, and sensor systems that prevent operation when safety measures are compromised. Prioritizing safety not only protects the operator but also minimizes the risk of costly damage to the machinery.
Advantages of Using CNC Lathes in Metal Fabrication
CNC lathes offer numerous advantages over traditional manual lathes, making them the preferred choice in metal fabrication:
- Precision and Accuracy: CNC lathes provide unprecedented accuracy, ensuring parts are machined to tight tolerances.
- Repeatability: Once a program is set, CNC lathes can reproduce identical parts with minimal deviation, ideal for mass production.
- Efficiency: CNC machines operate with higher speeds and can run unattended, increasing overall productivity.
- Complex Shapes: CNC lathes can create complex geometries that would be difficult or impossible to achieve manually.
- Reduced Waste: Advanced CNC programming enhances material utilization, reducing the overall waste produced during machining.
Common Applications of CNC Lathes
CNC lathes are versatile machines used in a variety of applications. Here are some common industries and products that utilize these machines:
1. Aerospace Industry
In the aerospace sector, precision is paramount. CNC lathes are utilized to manufacture parts like turbine components, landing gear parts, and engine mounts, ensuring each piece meets strict safety and performance standards.
2. Automotive Manufacturing
The automotive industry relies heavily on CNC lathes for producing engine components, transmission parts, and fittings. High accuracy in these parts is essential for vehicle performance and safety.
3. Medical Device Production
With the demand for precision instruments in healthcare, CNC lathes are used to create surgical tools, implants, and other medical components that require exact specifications and tolerances.
4. Electronics and Appliance Manufacturing
CNC lathe technology is also employed in manufacturing electrical contacts and components for various household appliances, contributing to the growing demand for durable and reliable products.
Conclusion
In summary, the parts of a CNC lathe work together to facilitate the precise and efficient machining of components across various industries. By understanding each component's role, operators can leverage the full potential of CNC lathes in metal fabrication. As technology continues to evolve, gaining knowledge in CNC operations will be essential for any manufacturing business aiming for excellence. Embracing this technological innovation not only enhances production capabilities but also sets the foundation for meeting the demands of an ever-evolving marketplace.
For businesses in need of high-quality CNC lathe machining services, DeepMould.net offers unparalleled expertise and advanced solutions tailored to your specific requirements.