Understanding Die Casting Machine Parts
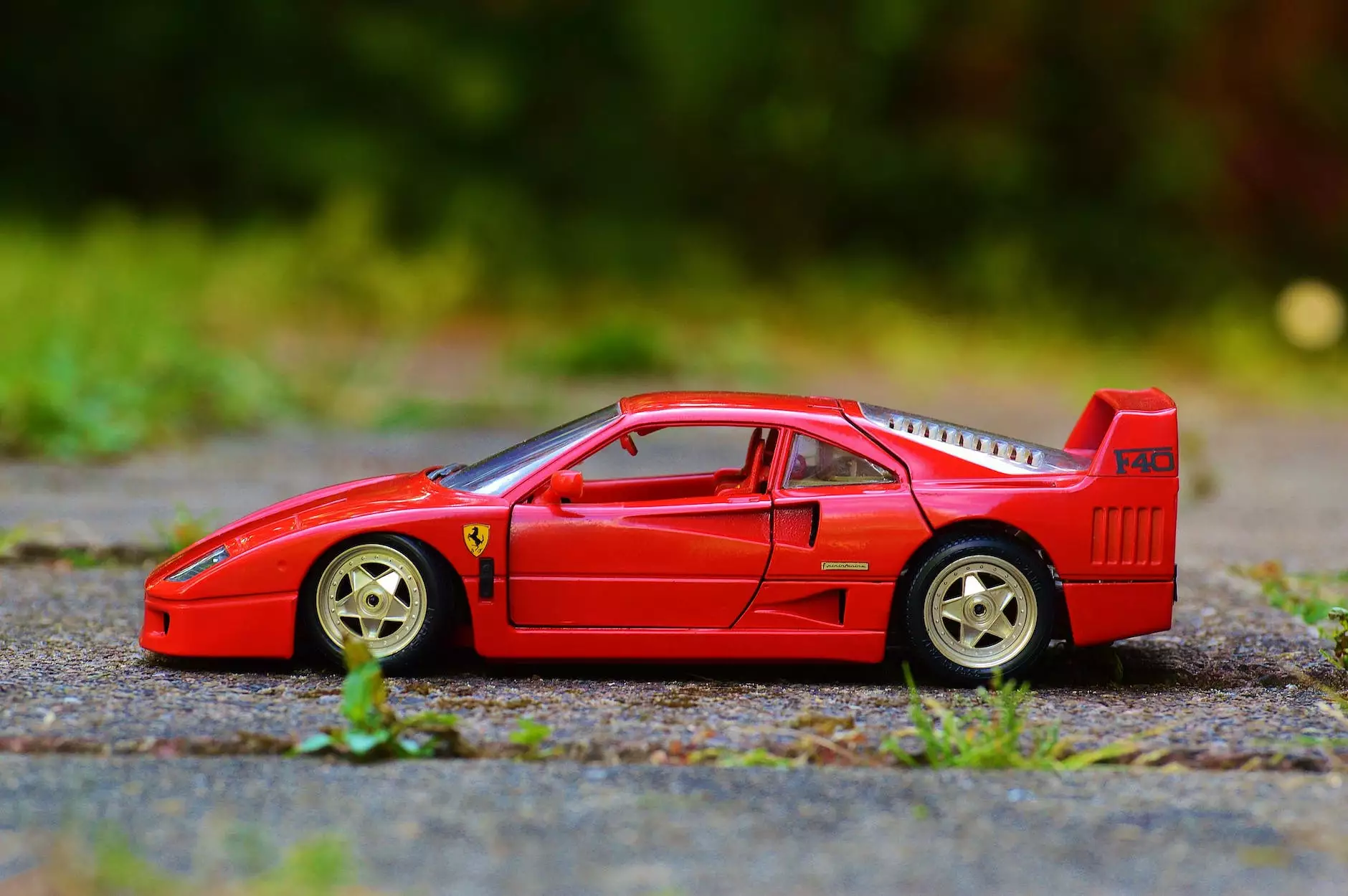
In the ever-evolving world of metal fabrication, understanding the core components that drive production efficiency is essential. One of the pivotal aspects of this industry is the use of die casting machine parts. These components play a critical role in various manufacturing processes, impacting both the volume and quality of products produced. In this article, we will delve into the various aspects of die casting machine parts, their functionality, and their significance in modern manufacturing.
What is Die Casting?
Die casting is a manufacturing process that involves forcing molten metal into a mold cavity. The process is used to create parts with a high degree of precision, making it highly suitable for industries such as automotive, aerospace, and electronics. The die casting process itself relies heavily on a variety of critical machine parts that ensure optimal performance and reliability. Let's explore these parts in-depth.
Key Components of Die Casting Machines
Die casting machines, fundamentally, are composed of various parts, each playing a unique role in the production process. Below are some of the essential die casting machine parts:
- Injection System: This includes the injection unit that melts the metal and injects it into the die.
- Clamping Unit: This part holds the die in place during the injection process. It is designed to withstand high pressure without compromising stability.
- Cooling System: Essential for regulating temperature, the cooling system helps the molten metal solidify and ensures that the die does not overheat.
- Control System: Modern die casting machines come equipped with sophisticated control systems that manage the entire operation through programmable logic controllers (PLCs).
- Die or Mold: The die is the metallic cavity into which the melted metal is injected. It shapes the final part using high precision.
- Ejector System: After cooling and solidification, this system helps eject the finished part from the die.
The Importance of Quality Die Casting Machine Parts
Using high-quality die casting machine parts is crucial for several reasons:
- Precision Production: Quality parts ensure that the machine operates accurately, producing components that meet exact specifications.
- Reduced Downtime: Reliable parts minimize the chances of mechanical failure, ensuring that production lines run smoothly.
- Longer Lifespan: Robust and well-engineered parts extend the operational life of machines, making them a cost-effective choice in the long run.
- Improved Surface Finish: High-quality parts contribute to a better surface finish of the die-cast components, crucial for aesthetic and functional productions.
- Efficiency in Production: The performance of die casting machines directly affects manufacturing efficiency. Quality parts enable faster cycles and less scrap.
Challenges in Die Casting Machine Parts
While die casting is a highly effective manufacturing process, it is not without its challenges. Managing the quality and performance of die casting machine parts is critical to overcoming these issues:
- Wear and Tear: Over time, moving parts may wear out, requiring regular maintenance and replacement to uphold performance.
- Thermal Fatigue: Continuous exposure to high temperatures can lead to the degradation of certain components, particularly in the clamping and injection systems.
- Quality Control: Implementing robust quality control processes is essential in ensuring that every part used in the die casting process meets industry standards.
- Technological Advancements: Keeping up with the latest technologies in die casting requires ongoing investment in new components and systems.
Advancements in Die Casting Technology
The die casting industry is witnessing rapid technological advancements that enhance the production and performance of die casting machines. Innovations include:
- Automatic Systems: Automation in die casting machines is increasing, enabling higher productivity levels and reducing labor costs.
- Smart Manufacturing: The integration of IoT devices allows for real-time monitoring and data collection, improving machine performance and predictive maintenance.
- 3D Printing for Molds: The use of 3D printing technology to create molds offers design flexibility and faster prototyping.
- High-Pressure Die Casting: Newer machines are capable of applying higher pressures for improved metal flow and filling, leading to better component quality.
Choosing the Right Die Casting Machine Parts for Your Business
When selecting die casting machine parts for your operations, it is crucial to consider several factors:
- Material Quality: Ensure that the materials used in manufacturing the parts are of high quality and suitable for the specific application.
- Compatibility: Choose parts that are compatible with your existing machine to avoid operational inefficiencies.
- Supplier Reliability: Partner with reputable suppliers who offer warranties and support for their products.
- Cost vs. Value: While initial costs can be an influential factor, consider the long-term value and maintenance costs associated with the parts.
Conclusion
The importance of die casting machine parts in the realm of metal fabrication cannot be overstated. From ensuring the accuracy of production to maintaining operational efficiency, these components are vital to success in the manufacturing sector. By investing in high-quality parts and keeping abreast of technological advancements, businesses can significantly improve their production quality and efficiency. The future of die casting remains bright, with ongoing innovations set to enhance capabilities and meet the demands of an increasingly competitive market.
As you explore options for optimizing your die casting processes, always remember that the quality of the components you choose plays a decisive role in determining the success and reliability of your manufacturing efforts.